Best Crucible For Copper casting and long service life
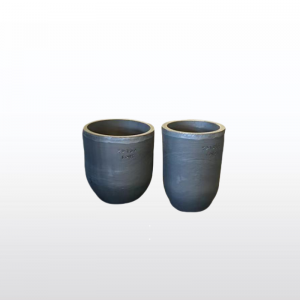
Best Crucible For Copper
When it comes to melting copper and its alloys, selecting the Best Crucible For Copper is paramount for ensuring efficiency, quality, and safety in your foundry operations. Understanding the specific requirements and characteristics of copper melting crucibles will help you make an informed decision tailored to your needs.
Model |
No. |
H |
OD |
BD |
RA100 | 100# | 380 | 330 | 205 |
RA200H400 | 180# | 400 | 400 | 230 |
RA200 | 200# | 450 | 410 | 230 |
RA300 | 300# | 450 | 450 | 230 |
RA350 | 349# | 590 | 460 | 230 |
RA350H510 | 345# | 510 | 460 | 230 |
RA400 | 400# | 600 | 530 | 310 |
RA500 | 500# | 660 | 530 | 310 |
RA600 | 501# | 700 | 530 | 310 |
RA800 | 650# | 800 | 570 | 330 |
RR351 | 351# | 650 | 420 | 230 |
Key Features of the Best Crucible For Copper
- High Heat Resistance: The ideal crucible for melting copper must withstand temperatures exceeding 1,600°C. Graphite silicon carbide crucibles are renowned for their exceptional high-temperature resistance, ensuring they remain structurally sound during the melting process.
- Excellent Thermal Conductivity: Effective heat transfer is crucial for the efficient melting of copper. The graphite silicon carbide material allows for rapid and uniform heat distribution, significantly improving smelting efficiency and reducing processing time.
- Corrosion Resistance: Copper melting processes often expose crucibles to acidic or alkaline substances. A high-quality crucible made from graphite silicon carbide boasts strong corrosion resistance, which extends its service life and minimizes the risk of contamination in the molten metal.
- Mechanical Strength: Maintaining structural integrity under high temperatures is critical. The best crucibles for copper feature high mechanical strength, ensuring they do not deform or sustain damage during intense thermal conditions.
- Stability During Use: Chemical and physical stability is essential to prevent unwanted reactions between the crucible and molten copper. This stability contributes to maintaining the purity of the molten metal, which is vital in producing high-quality copper products.
Ideal Applications
The Best Crucible For Copper is suitable for various applications, including:
- Copper Melting: Crucibles are designed specifically for melting copper and its alloys, ensuring efficient smelting and minimal metal loss.
- Brass and Bronze Casting: These crucibles can also be effectively utilized for melting brass and bronze, taking advantage of their high heat resistance and chemical stability.
- Metal Recycling: Ideal for facilities focused on recycling copper, these crucibles help maintain material integrity and optimize the recycling process.
Maintenance and Best Practices
To maximize the lifespan and performance of your copper crucible, consider the following maintenance tips:
- Proper Preheating: Ensure proper preheating to prevent thermal shock, which can lead to cracking. Gradually raise the temperature, avoiding rapid fluctuations.
- Regular Cleaning: After each use, promptly clean the crucible to prevent residue buildup, which can affect future melts.
- Avoid Acidic Exposure: Do not immerse the crucible in acidic solutions for extended periods, as this can lead to premature wear.
- Monitor for Damage: Regularly inspect the crucible for any signs of damage or degradation, replacing it as necessary to maintain safety and efficiency.
Conclusion
Choosing the Best Crucible For Copper involves understanding the specific demands of your melting process. With the right crucible, you can enhance your operational efficiency, reduce downtime, and ensure the quality of your melted copper and alloys. Consider investing in high-quality graphite silicon carbide crucibles designed for optimal performance in demanding environments.