Continuous casting Crucible Bottom Pouring for continuous casting process
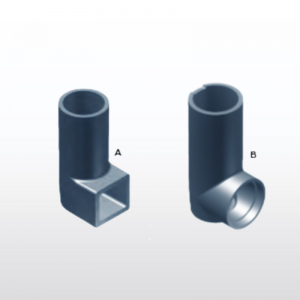
continuous casting crucible
1. Introduction to Continuous Casting Crucibles:
In the continuous casting process, choosing the right crucible is crucial for ensuring precision and efficiency. Our Continuous Casting Crucibles are specifically engineered for seamless performance during high-temperature metal melting operations. Whether you are working with graphite crucibles with pour spouts or silicon carbide graphite pots, we have the perfect solution for your needs. Our pouring crucibles ensure smooth metal flow and reduce waste during the casting process.
2. Key Features of Continuous Casting Crucibles:
- High Thermal Conductivity: Our crucibles ensure even heat distribution, which is vital for maintaining consistent metal flow during continuous casting.
- Temperature Resistance: Designed to withstand high temperatures, these crucibles are perfect for melting various metals, including copper, brass, and steel.
- Customization: We offer a wide range of sizes and designs to suit specific casting needs, including silicon carbide crucibles with spouts for easier metal pouring.
3. Advantages of Using Continuous Casting Crucibles:
- Efficient Metal Flow: Our Graphite Crucibles with Pour Spouts provide excellent control over molten metal flow, making them ideal for precision casting operations.
- Durability: Made from high-quality materials like graphite and silicon carbide, these crucibles offer superior resistance to wear and oxidation, significantly extending their lifespan.
- Versatility: Suitable for melting a variety of metals such as aluminum, copper, brass, and steel, our crucibles provide flexible solutions for different industrial applications.
4. Application of Continuous Casting Crucibles:
Our Continuous Casting Crucibles are widely used in industries such as:
- Metallurgy: For smelting and refining metals like copper, brass, and steel.
- Foundries: Ideal for continuous casting operations in foundries where precision and control are critical.
- Metal Processing Plants: Perfect for large-scale metal melting operations, ensuring efficiency and minimizing downtime.
5. Detailed Dimensions and Specifications:
Our crucibles are available in various sizes to accommodate different industrial needs. Below is a summary of the dimensions for some of our continuous casting crucibles:
Shape/Form | A (mm) | B (mm) | C (mm) | D (mm) | E x F max (mm) | G x H (mm) |
---|---|---|---|---|---|---|
A | 650 | 255 | 200 | 200 | 200x255 | Upon request |
A | 1050 | 440 | 360 | 170 | 380x440 | Upon request |
B | 1050 | 440 | 360 | 220 | ⌀380 | Upon request |
B | 1050 | 440 | 360 | 245 | ⌀440 | Upon request |
A | 1500 | 520 | 430 | 240 | 400x520 | Upon request |
B | 1500 | 520 | 430 | 240 | ⌀400 | Upon request |
Final specifications can be customized according to customer needs.
6. User Guide for Continuous Casting Crucibles:
To maximize the service life of your crucibles and ensure the best performance:
- Storage: Store in a dry area to prevent moisture damage.
- Handling: Use appropriate handling tools to avoid damaging the crucible.
- Installation: Properly position the crucible in the furnace, ensuring it's centered for even heating and metal flow.
- Maintenance: Regularly inspect for wear and clean any slag or carbon buildup to avoid damaging the crucible.
Conclusion and Call to Action
Our Continuous Casting Crucibles offer the perfect combination of durability, efficiency, and precision for all your metal melting needs. Whether you're in metallurgy, foundry work, or large-scale metal processing, our crucibles ensure consistent performance and longevity.
Contact us today to learn more about our customizable crucible solutions and how we can help improve your casting processes with our high-performance products.