Cylindrical crucible used in induction furnace and gas furnace
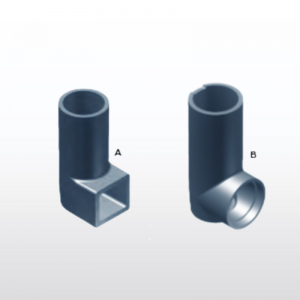
Introducing our high performance silicon carbide crucibles
Material:
Our Cylindrical Crucible is crafted from isostatically pressed silicon carbide graphite, a material that offers exceptional high-temperature resistance and excellent thermal conductivity, making it an essential tool for industrial smelting applications.
- Silicon Carbide (SiC): Silicon carbide is known for its extreme hardness and excellent resistance to wear and corrosion. It can withstand high-temperature chemical reactions, offering superior stability even under thermal stress, which reduces the risk of cracking during sudden temperature changes.
- Natural Graphite: Natural graphite delivers exceptional thermal conductivity, ensuring rapid and uniform heat distribution throughout the crucible. Unlike traditional clay-based graphite crucibles, our cylindrical crucible uses high-purity natural graphite, which improves heat transfer efficiency and reduces energy consumption.
- Isostatic Pressing Technology: The crucible is formed using advanced isostatic pressing, ensuring uniform density with no internal or external defects. This technology enhances the strength and crack resistance of the crucible, extending its durability in high-temperature environments.
Shape/Form | A (mm) | B (mm) | C (mm) | D (mm) | E x F max (mm) | G x H (mm) |
---|---|---|---|---|---|---|
A | 650 | 255 | 200 | 200 | 200x255 | Upon request |
A | 1050 | 440 | 360 | 170 | 380x440 | Upon request |
B | 1050 | 440 | 360 | 220 | ⌀380 | Upon request |
B | 1050 | 440 | 360 | 245 | ⌀440 | Upon request |
A | 1500 | 520 | 430 | 240 | 400x520 | Upon request |
B | 1500 | 520 | 430 | 240 | ⌀400 | Upon request |
Final specifications can be customized according to customer needs.
Performance:
- Superior Thermal Conductivity: The Cylindrical Crucible is made from high thermal conductivity materials that allow for rapid and even heat distribution. This enhances the efficiency of the smelting process while reducing energy consumption. Compared to conventional crucibles, thermal conductivity is improved by 15%-20%, leading to significant fuel savings and faster production cycles.
- Excellent Corrosion Resistance: Our silicon carbide graphite crucibles are highly resistant to the corrosive effects of molten metals and chemicals, ensuring the stability and longevity of the crucible during prolonged use. This makes them ideal for smelting aluminum, copper, and various metal alloys, reducing maintenance and replacement frequency.
- Extended Service Life: With its high-density and high-strength structure, the lifespan of our cylindrical crucible is 2 to 5 times longer than traditional clay graphite crucibles. The superior resistance to cracking and wear extends operational life, lowering downtime and replacement costs.
- High Oxidation Resistance: A specially formulated material composition effectively prevents oxidation of the graphite, minimizing degradation at high temperatures and further extending the crucible's life.
- Superior Mechanical Strength: Thanks to the isostatic pressing process, the crucible boasts exceptional mechanical strength, retaining its shape and durability in high-temperature environments. This makes it ideal for smelting processes requiring high pressure and mechanical stability.
Product Advantages:
- Material Benefits: The use of natural graphite and silicon carbide ensures high thermal conductivity and corrosion resistance, providing lasting performance in harsh, high-temperature environments.
- High-Density Structure: Isostatic pressing technology eliminates internal voids and cracks, significantly improving the crucible’s durability and strength during extended use.
- High-Temperature Stability: Capable of withstanding temperatures up to 1700°C, this crucible is ideal for various smelting and casting processes involving metals and alloys.
- Energy Efficiency: Its superior heat transfer properties reduce fuel consumption, while the environmentally friendly material minimizes pollution and waste.
Choosing our high-performance Cylindrical Crucible will not only enhance your smelting efficiency but also reduce energy consumption, extend equipment lifespan, and lower maintenance costs, ultimately improving production efficiency.
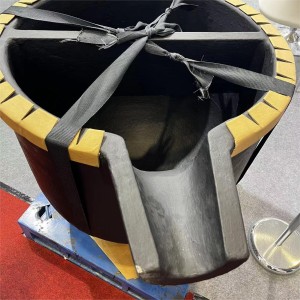