Foundry Crucibles for Aluminium Continuous Casting Process
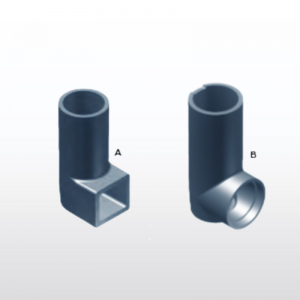
Advantages and preheating process of silicon carbide crucible
Introduction:
Foundry crucibles play a crucial role in the metal smelting and casting industries, providing high-temperature resistance and durability. Our Foundry Crucibles, available in both silicon carbide and graphite variants, are engineered to meet the demanding needs of metalworkers, ensuring optimal performance in various applications.
Product Features of Foundry Crucibles:
Feature | Description |
---|---|
Thermal Conductivity | Made from high thermal conductivity materials, these crucibles facilitate rapid heat conduction. |
Long Service Life | Silicon carbide crucibles offer a service life 2-5 times longer than traditional clay graphite options. |
High Density | Manufactured using advanced isostatic pressing to ensure uniform density and defect-free material. |
High Strength | High-pressure molding techniques enhance strength, making them suitable for extreme conditions. |
Corrosion Resistance | Designed to withstand the corrosive effects of molten metals, extending their usability. |
Low Slag Adhesion | Minimal slag adhesion on the inner walls reduces heat resistance and prevents expansion. |
High Temperature Resistance | Capable of operating in temperatures ranging from 400°C to 1700°C, suitable for various smelting processes. |
Low Pollution | Engineered to minimize harmful impurities during metal smelting. |
Metal Anti-Corrosion | Contains special elements that effectively inhibit metal oxidation. |
Energy Saving and Environmental Protection | Efficient heat conduction helps reduce fuel consumption and minimizes waste pollution. |
High Oxidation Resistance | Advanced antioxidant mechanisms protect the crucible's integrity during use. |
Importance of Preheating Process:
Proper preheating is essential for ensuring the longevity of silicon carbide crucibles. Neglecting this step can lead to premature failure. Here’s a recommended preheating procedure:
- 0°C-200°C: Oil slow heating for 4 hours, electric slow heating for 1 hour.
- 200°C-300°C: Energize and heat slowly for 4 hours.
- 300°C-800°C: Slow heating for 4 hours.
- After Furnace Shutdown: Follow gradual reheating guidelines to maintain crucible integrity.
Product Applications:
Our foundry crucibles are versatile and can be utilized across various industries, including:
- Aluminum Alloy Production: Critical for high-quality aluminum alloy fabrication.
- Metalworking Processes: Essential tools for foundries and metal recyclers.
Maintenance Tips:
To maximize the life and performance of your foundry crucibles, adhere to the following maintenance practices:
- Regular cleaning to prevent buildup of contaminants.
- Proper preheating before each use to avoid thermal shock.
Frequently Asked Questions (FAQ):
- What temperatures can foundry crucibles withstand?
Our crucibles are designed to endure temperatures up to 1700 degrees Celsius. - How important is preheating?
Preheating is vital to prevent cracks and ensure optimal performance. - What maintenance is required for foundry crucibles?
Regular cleaning and proper preheating are essential for maintaining crucible integrity.
Conclusion:
Utilizing our Foundry Crucibles will enhance your metal smelting and casting operations. Their superior features, coupled with the essential preheating process, guarantee durability and optimal performance in demanding environments.
Call to Action (CTA):
Contact us today for personalized recommendations or to place your order for our top-quality foundry crucibles. Elevate your metalworking processes with our reliable and efficient solutions!