Melting crucible for non-ferrous metal Melting and Casting
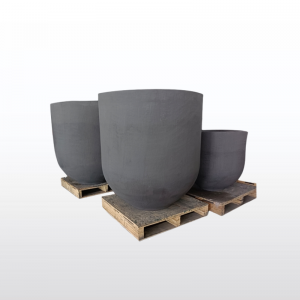
melting crucibles
In the metal melting industry, particularly for foundries and smelting operations, choosing the right crucible is essential for efficiency and product quality. Professionals in metalworking, particularly those involved in aluminum and its alloys, need a melting crucible that delivers reliability and performance. This introduction will explore the features, specifications, and advantages of our Crucible For Foundry and Crucible For Metal Melting, ensuring you make an informed decision for your operations.
Key Features of Our Melting Crucibles
- Crucible Materials:
- Silicon Carbide Crucibles: Known for their excellent thermal conductivity, these crucibles can operate effectively at temperatures up to 1700°C, far exceeding the melting point of aluminum (660.37°C). Their high-density structure provides remarkable strength and resistance to deformation.
- Carbonized Silicon Carbide Crucibles: An improved version that addresses common weaknesses found in traditional crucibles, such as low strength and poor thermal shock resistance. These crucibles utilize a composite of carbon fiber and silicon carbide, ensuring superior performance.
- Best Crucible Material:
- Our silicon carbide crucibles offer outstanding characteristics, including:
- Melting Point: Up to 2700°C, suitable for various high-temperature applications.
- Density: 3.21 g/cm³, contributing to their robust mechanical strength.
- Thermal Conductivity: 120 W/m·K, enabling fast and uniform heat distribution for improved melting efficiency.
- Thermal Expansion Coefficient: 4.0 × 10⁻⁶/°C in the range of 20-1000°C, minimizing thermal stress.
- Our silicon carbide crucibles offer outstanding characteristics, including:
- Crucible Temperature Range:
- Our crucibles are designed to withstand an operating temperature range of 800°C to 2000°C with an instantaneous maximum temperature resistance of 2200°C, ensuring safe and efficient melting of various metals.
Specifications (Customizable)
No | Model | OD | H | ID | BD |
36 | 1050 | 715 | 720 | 620 | 300 |
37 | 1200 | 715 | 740 | 620 | 300 |
38 | 1300 | 715 | 800 | 640 | 440 |
39 | 1400 | 745 | 550 | 715 | 440 |
40 | 1510 | 740 | 900 | 640 | 360 |
41 | 1550 | 775 | 750 | 680 | 330 |
42 | 1560 | 775 | 750 | 684 | 320 |
43 | 1650 | 775 | 810 | 685 | 440 |
44 | 1800 | 780 | 900 | 690 | 440 |
45 | 1801 | 790 | 910 | 685 | 400 |
46 | 1950 | 830 | 750 | 735 | 440 |
47 | 2000 | 875 | 800 | 775 | 440 |
48 | 2001 | 870 | 680 | 765 | 440 |
49 | 2095 | 830 | 900 | 745 | 440 |
50 | 2096 | 880 | 750 | 780 | 440 |
51 | 2250 | 880 | 880 | 780 | 440 |
52 | 2300 | 880 | 1000 | 790 | 440 |
53 | 2700 | 900 | 1150 | 800 | 440 |
54 | 3000 | 1030 | 830 | 920 | 500 |
55 | 3500 | 1035 | 950 | 925 | 500 |
56 | 4000 | 1035 | 1050 | 925 | 500 |
57 | 4500 | 1040 | 1200 | 927 | 500 |
58 | 5000 | 1040 | 1320 | 930 | 500 |
- Thickness Reduction: Our carbonized silicon carbide crucibles are designed with a thickness reduction of 30%, enhancing thermal conductivity while maintaining strength.
- Increased Strength: The strength of our crucibles is increased by 50%, enabling them to withstand higher mechanical stress.
- Thermal Shock Resistance: Enhanced by 40%, minimizing the likelihood of cracking during rapid heating and cooling.
Manufacturing Process
The manufacturing process for our carbonized silicon carbide crucibles involves several critical steps:
- Preform Creation: Carbon fiber is preprocessed into a form suitable for crucible production.
- Carbonization: This step establishes the initial silicon carbide structure.
- Densification and Purification: Further carbonization increases the material density and chemical stability.
- Siliconing: The crucible is dipped into molten silicon to enhance its strength and corrosion resistance.
- Final Shaping: The crucible is shaped to meet specific requirements, ensuring optimal performance.
Advantages and Performance
- High-Temperature Strength: With the capability to maintain structural integrity at extreme temperatures, our silicon carbide crucibles ensure reliability during high-temperature melting processes.
- Corrosion Resistance: These crucibles resist corrosion from molten aluminum and other metals, significantly extending their lifespan and reducing replacement frequency.
- Chemically Inert: Silicon carbide does not react with aluminum, ensuring the purity of the molten metal and preventing contamination from impurities.
- Mechanical Strength: With a bending strength of 400-600 MPa, our crucibles can withstand heavy loads, making them suitable for demanding applications.
Applications
Silicon carbide melting crucibles are widely utilized in:
- Aluminum Smelting Plants: Essential for melting and purifying aluminum ingots, ensuring high-quality aluminum products.
- Aluminum Alloy Foundries: Providing stable high-temperature environments for the casting of aluminum alloy parts, improving product quality and reducing scrap rates by 30%.
- Laboratories and Research Institutions: Ideal for high-temperature experiments, ensuring accurate data and reliable results due to their chemical inertness and thermal stability.
Conclusion
Our melting crucibles are indispensable tools in the foundry and metal melting industries, known for their exceptional performance and versatility. By prioritizing quality and continuous innovation, we are committed to providing our customers with the highest-quality melting solutions tailored to their specific needs. If you are in search of a reliable crucible for your metal melting operations, look no further than our silicon carbide crucibles designed with precision and expertise. For inquiries or further information, please feel free to contact us.