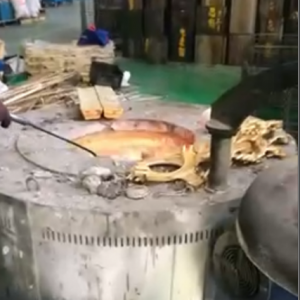
Brass is a very important copper alloy, with its excellent mechanical properties, good corrosion resistance and easy processing characteristics, in hardware, bathroom, Musical Instruments, electronics and many other industries have a wide range of applications. As the key equipment in the process of brass processing, the performance of brass melting furnace is directly related to the quality of brass products and the speed of production efficiency.
In recent years, with the continuous progress of science and technology, high-frequency induction melting furnace has gradually replaced the traditional melting furnace and become the preferred choice of copper smelting furnace. So, what are the advantages of our electric induction furnace? How does it promote the development of the brass processing industry?
High frequency industrial induction furnace: principles and advantages
The high-frequency induction melting furnace uses the principle of electromagnetic induction, and generates eddy currents in the metal charge through high-frequency alternating current, so as to quickly realize the heating and melting of the metal. Compared with traditional melting furnaces, it has the following obvious advantages:
High efficiency and energy saving: high-frequency induction heating can directly act on the metal charge, and the thermal efficiency can reach more than 90%, and compared with the traditional melting furnace, it can save 30%-50% energy. Our high frequency induction furnace uses advanced energy saving technology, melting a ton of brass only requires 350 degrees of electricity, greatly reducing production costs.
Uniform heating: The electromagnetic induction heating method can allow the metal charge to be heated inside and outside at the same time, and the temperature distribution is uniform, effectively avoiding the local overheating or undercooling.
Environmental protection and pollution-free: Using electric energy as an energy source, it will not emit combustion exhaust gas during work, and the working environment is clean and tidy, meeting the relevant requirements of environmental protection.
Easy operation: high degree of automation, can achieve accurate temperature control, but also automatic feeding, automatic discharge, reduce labor costs.
Precise composition control: High frequency induction heating can effectively prevent the oxidation and burning of copper elements, thus ensuring the composition and performance of brass materials.
No water cooling system: Our high frequency induction melting furnaces use a unique air cooling design and do not require additional water cooling systems, saving equipment costs and maintenance costs, while avoiding waste of water resources.
Application of high frequency melting induction furnace in brass melting
The application of high frequency melting induction furnace in brass melting is mainly reflected in the following aspects:
Brass rod, brass tube, brass plate melting: high frequency induction melting furnace can quickly and evenly melt brass materials to meet the production needs of different sizes and shapes of brass products.
Production of brass castings: The high frequency induction melting furnace can precisely control the temperature and composition of brass liquid to ensure the quality and performance of the castings.
Recycling of brass waste: The high frequency induction melting furnace can efficiently recycle brass waste, reduce production costs, and improve the utilization of resources.
Reasons to choose high frequency induction melting furnace
Improve production efficiency: can quickly heat and melt, shorten the production cycle, improve production efficiency.
Reduce production costs: energy saving and environmental protection, reduce energy consumption and environmental pollution, and reduce production costs.
Improve product quality: the heating is uniform and the temperature can be controlled, effectively improving the quality of the product.
Achieve automated production: high degree of automation, can easily achieve automated production, reduce labor costs.
No water cooling system: saving equipment costs and maintenance costs, avoiding the waste of water resources.
Post time: Feb-21-2025