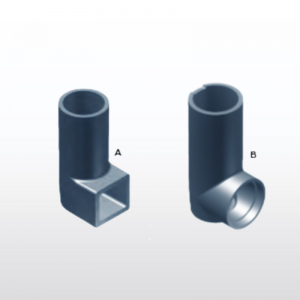
Introduction
What makes continuous casting so efficient? At its core lies one essential component: continuous casting crucibles. These specialized crucibles play a pivotal role in ensuring precision, durability, and efficiency in the production process, especially for materials like bronze and other alloys. Whether you're using silicon carbide bonding type crucibles or exploring furnace crucible materials, understanding their applications and benefits is key to making the right choice for your business.
1. What Is Continuous Casting?
Continuous casting is a method used to solidify molten metals into semi-finished shapes such as slabs, rods, or tubes. It's a go-to technique for industries producing bronze, aluminum, and steel. Unlike traditional casting methods, continuous casting ensures consistent quality and minimal waste.
2. The Importance of Continuous Casting Crucibles
Why are crucibles so critical?
- Durability: Withstand extreme temperatures.
- Thermal Conductivity: Essential for even heat distribution.
- Longevity: Reduce the frequency of replacements.
The right crucible material, such as silicon carbide bonding, ensures smoother operations and better results.
3. Material Insights: Why Silicon Carbide Bonding Type Is Ideal
The choice of furnace crucible material significantly impacts performance. Here’s why silicon carbide bonding type is a game-changer:
Feature | Silicon Carbide Crucibles | Other Materials |
---|---|---|
Thermal Conductivity | Excellent | Moderate |
Melting Point Tolerance | High | Varies |
Durability | Resistant to thermal shock | Susceptible to cracking |
Applications | Ideal for high-temp alloys | Limited to low-temp metals |
Silicon carbide graphite crucibles combine the strength of silicon carbide with the thermal properties of graphite, making them ideal for continuous casting molds.
4. Applications: From Bronze to High-Temperature Alloys
Continuous casting crucibles are widely used in industries dealing with:
- Bronze Casting: Ensures smooth pouring and uniform cooling.
- Upcast Casting Processes: For producing rods and wires.
- High-Temperature Alloys: Such as nickel and titanium.
They also work seamlessly with continuous casting molds, making them indispensable in modern foundries.
5. Crucible Maintenance and Care
Prolong the lifespan of your crucibles with these tips:
- Regular Inspection: Check for cracks or signs of wear.
- Proper Cleaning: Avoid using abrasive tools that may damage the surface.
- Controlled Heating and Cooling: Prevent thermal shock by gradually adjusting temperatures.
6. FAQs for Buyers
Q: What temperature range can continuous casting crucibles handle?
A: It depends on the material. For instance, silicon carbide bonding crucibles can handle temperatures up to 1,500°C.
Q: How do I choose the right crucible size?
A: Consider the type of metal, volume of molten material, and your furnace’s capacity.
Q: Can you customize crucibles for specific applications?
A: Yes, custom designs are available to suit unique production needs.
7. Why Choose Us for Your Crucible Needs?
We specialize in high-quality crucibles tailored for continuous casting. Here’s why we stand out:
- Premium Materials: Durable and efficient.
- Custom Solutions: Designed to match your exact requirements.
- Industry Expertise: Decades of experience in the foundry industry.
- Global Reach: Serving clients worldwide with reliable logistics.
Conclusion
Investing in the right continuous casting crucibles can elevate your foundry operations, ensuring efficiency and top-notch results. Ready to upgrade your casting process? Contact us today for expert guidance and premium products!
Would you like to see more details about our crucibles? Let us know!
Post time: Nov-29-2024