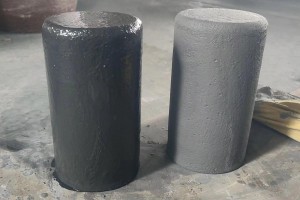
As an important tool in modern casting technology, silicon carbide crucible has gradually become the preferred container for non-ferrous metal smelting due to its excellent performance and unique material properties. Especially when processing high-temperature metal melts, silicon carbide crucibles exhibit a series of significant technical advantages. This article will introduce in detail the performance characteristics of silicon carbide crucibles, its application in casting processes, and how to provide efficient and reliable solutions for modern casting companies.
1. What is silicon carbide crucible?
Silicon carbide crucible is a high-temperature container using silicon carbide (SiC) as the main raw material. It is mainly used for smelting and processing various metals and alloys. Silicon carbide is a synthetic material with extremely high hardness and heat resistance. It is widely used in high-tech fields such as ceramics, metallurgy, and semiconductors.
Because silicon carbide crucibles have excellent physical and chemical properties such as high thermal conductivity, low thermal expansion coefficient, and corrosion resistance, they exhibit unparalleled stability and durability under high temperatures and extreme conditions.
2. Technical advantages of silicon carbide crucible
1. Excellent high temperature resistance
Silicon carbide crucibles have extremely high heat resistance and can withstand temperatures exceeding 1600°C. This makes them ideal for smelting high-temperature metals such as copper, aluminum and nickel. Compared with crucibles made of other materials, the strength of silicon carbide crucibles does not decrease significantly under high temperature conditions, ensuring its shape stability during the smelting process.
This excellent high-temperature resistance helps companies avoid crucibles from deforming or cracking due to high temperatures, thereby improving production continuity and efficiency.
2. Excellent thermal conductivity
Another notable feature of silicon carbide material is its high thermal conductivity, which allows for fast and even heat transfer. This means that during the smelting process, the molten metal can quickly reach the required temperature, reducing melting time and improving production efficiency.
This efficient heat conduction also reduces overheating of the molten metal, helping to achieve more precise temperature control during the casting process and ensuring consistent casting quality.
3. Low thermal expansion coefficient
The coefficient of thermal expansion refers to the extent to which a material expands in volume when heated. Silicon carbide has an extremely low coefficient of thermal expansion, which means it changes very little in size when heated. Therefore, even in an environment with severe temperature fluctuations, the silicon carbide crucible can maintain its original shape and avoid cracks or damage due to expansion or contraction.
The low thermal expansion is particularly suitable for casting processes involving frequent heating and cooling cycles, significantly extending the service life of the crucible.
4. Excellent corrosion resistance
During the smelting process, the molten metal reacts with the crucible, gradually eroding its surface. However, silicon carbide material has excellent chemical corrosion resistance and can effectively resist the erosion of metal liquids, especially when dealing with highly reactive metals such as copper and aluminum.
Good corrosion resistance not only extends the service life of the crucible, but also reduces impurity pollution caused by corrosion on the crucible surface, ensuring the purity of the metal liquid and improving the quality of the final product.
5. High mechanical strength
Silicon carbide crucibles maintain high mechanical strength even at high temperatures, making them less likely to break or deform. This high-strength characteristic enables the crucible to withstand the impact of molten metal and external mechanical stress, maintaining structural stability during high-temperature smelting.
6. Good thermal shock stability
Thermal shock stability refers to the ability of a material to resist cracking when the temperature changes rapidly. Silicon carbide crucibles exhibit excellent thermal shock stability and are able to withstand rapid temperature changes without cracking. This is particularly important for casting processes that require frequent heating and cooling.
three. Application of silicon carbide crucible
Due to its outstanding high temperature resistance, thermal conductivity, and corrosion resistance, silicon carbide crucibles are widely used in various metal smelting and casting processes, especially in the smelting of non-ferrous metals and alloys. The following are several common application scenarios:
Copper casting: When smelting copper, silicon carbide crucibles can keep the melt temperature uniform, reduce the formation of impurities, and improve the quality of copper parts.
Aluminum and aluminum alloy smelting: Aluminum easily reacts with the crucible during the smelting process, but the corrosion resistance of silicon carbide effectively protects the crucible from aluminum corrosion and extends its service life.
Other high-temperature smelting: Silicon carbide crucible is also suitable for smelting high-temperature metals such as zinc and nickel, and has strong adaptability.
Four. Use and maintenance of silicon carbide crucible
To extend the service life of silicon carbide crucibles, correct use and maintenance are crucial. Here are some suggestions:
Preheat the crucible: Before initial use or reuse, it is recommended to gradually preheat the crucible to operating temperature to prevent sudden heating and rupture.
Avoid rapid heating and cooling: Although silicon carbide crucibles have good thermal shock stability, too rapid temperature changes can still damage the crucible.
Regular inspection: During use, regularly check the crucible surface for signs of cracks or corrosion, and resolve potential problems in a timely manner.
Post time: Sep-05-2024