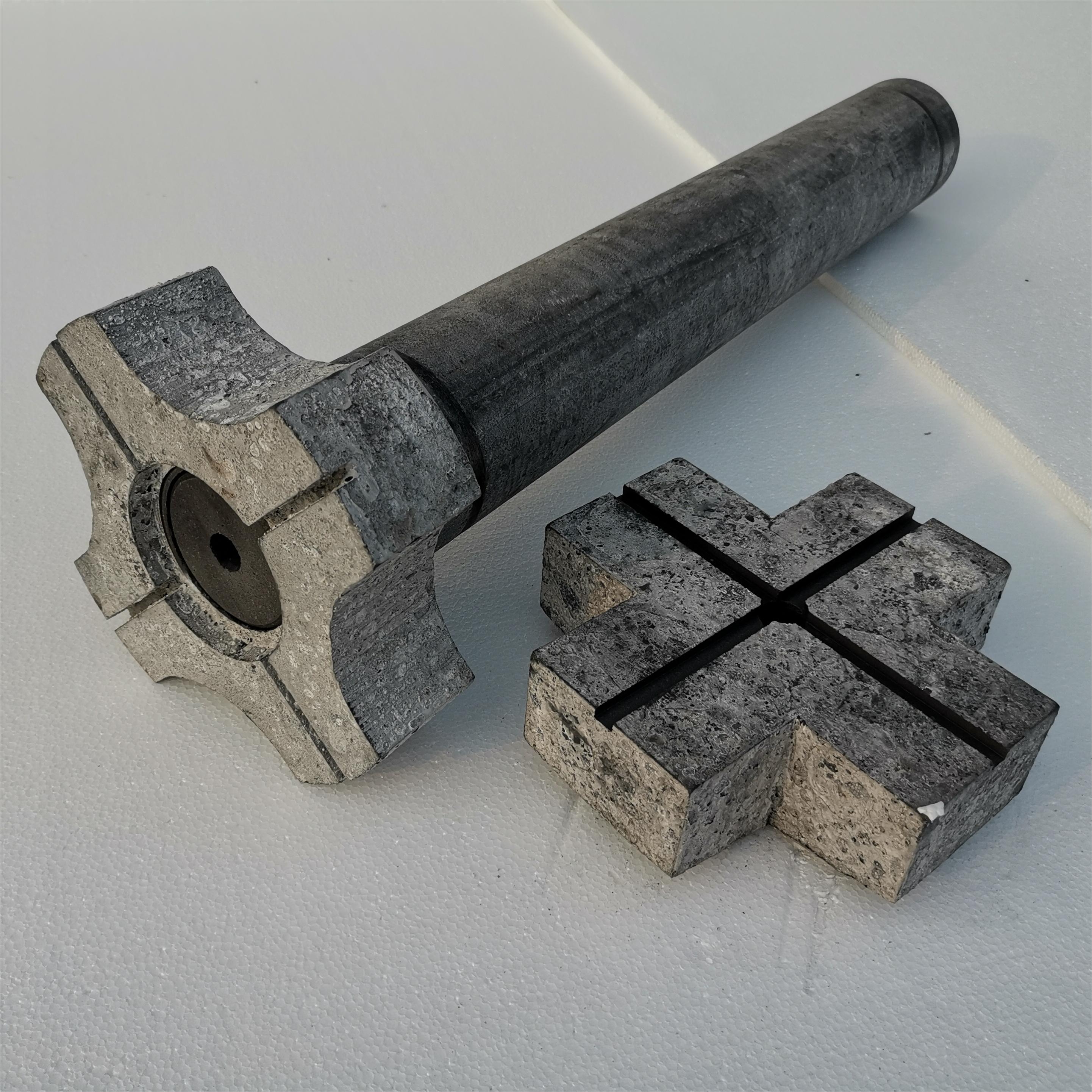
Our company's newly launched anti-oxidation graphite degassing rotor made of high-purity graphite has attracted widespread attention in the market. The degassing rotor not only effectively improves the purification effect of aluminum alloy melt, but also significantly extends the service life of the equipment, bringing significant economic benefits to aluminum alloy production enterprises.
The anti-oxidation degassing rotor is made of high-purity graphite, and the quality of the graphite directly affects the durability of the rotor. Through special processing technology and the application of anti-oxidation protective coating on the surface, the service life of the rotor is extended from the traditional 30 days to 50-60 days, greatly improving the operating efficiency of the equipment.
The main purpose of the degassing rotor is to purify liquid aluminum alloy. The purification process of liquid aluminum alloy is an important means to improve the comprehensive performance of aluminum alloy. In this process, a degassing rotor is used to mix the purification gas and solvent, and then blow it into the aluminum melt through a rotating injection method. This is considered to be the most advanced technology at present. The working principle of the degassing rotor is based on a system consisting of a rotor rod and a nozzle, which disperses argon or nitrogen into countless small bubbles at high speed and disperses them in the molten metal. These bubbles absorb hydrogen and oxides in the melt through the principles of gas pressure difference and surface adsorption, and finally bring them out of the melt surface to achieve purification.
In terms of use and maintenance, special attention needs to be paid to the following points:
The rotating nozzle of the degassing rotor is made of high-purity graphite, which is designed to disperse bubbles and use centrifugal force to evenly mix the gas-liquid flow, thereby increasing the contact area and time between bubbles and aluminum alloy liquid, and enhancing the purification effect.
After processing, the high temperature resistant degassing rotor has a service life of 55-65 days at 700°C and 25-35 days at 1000°C. The application of surface protective coating further extends its service life to 50-60 days.
In order to extend the service life of the degassing rotor, it is recommended to preheat it for 5-10 minutes at a position about 100mm away from the liquid surface before immersing it in the aluminum liquid to avoid the impact of rapid cooling on the material. The gas should be introduced before the rotor is immersed in the liquid, and the gas supply should be stopped after the rotor leaves the liquid surface to prevent the nozzle from clogging.
The main cause of damage to degassing rotors is high-temperature oxidation. Graphite will undergo significant oxidation in air at temperatures exceeding 600°C, forming CO and CO2 gases, causing the rotor diameter to gradually decrease until it breaks and becomes unusable.
By optimizing the material and processing technology of the degassing rotor, this product shows excellent performance and economic benefits in the field of aluminum liquid purification, marking a new height in aluminum alloy production technology. Manufacturing companies choosing this type of degassing rotor can not only improve production efficiency, but also effectively reduce equipment maintenance costs, which is worthy of widespread application.
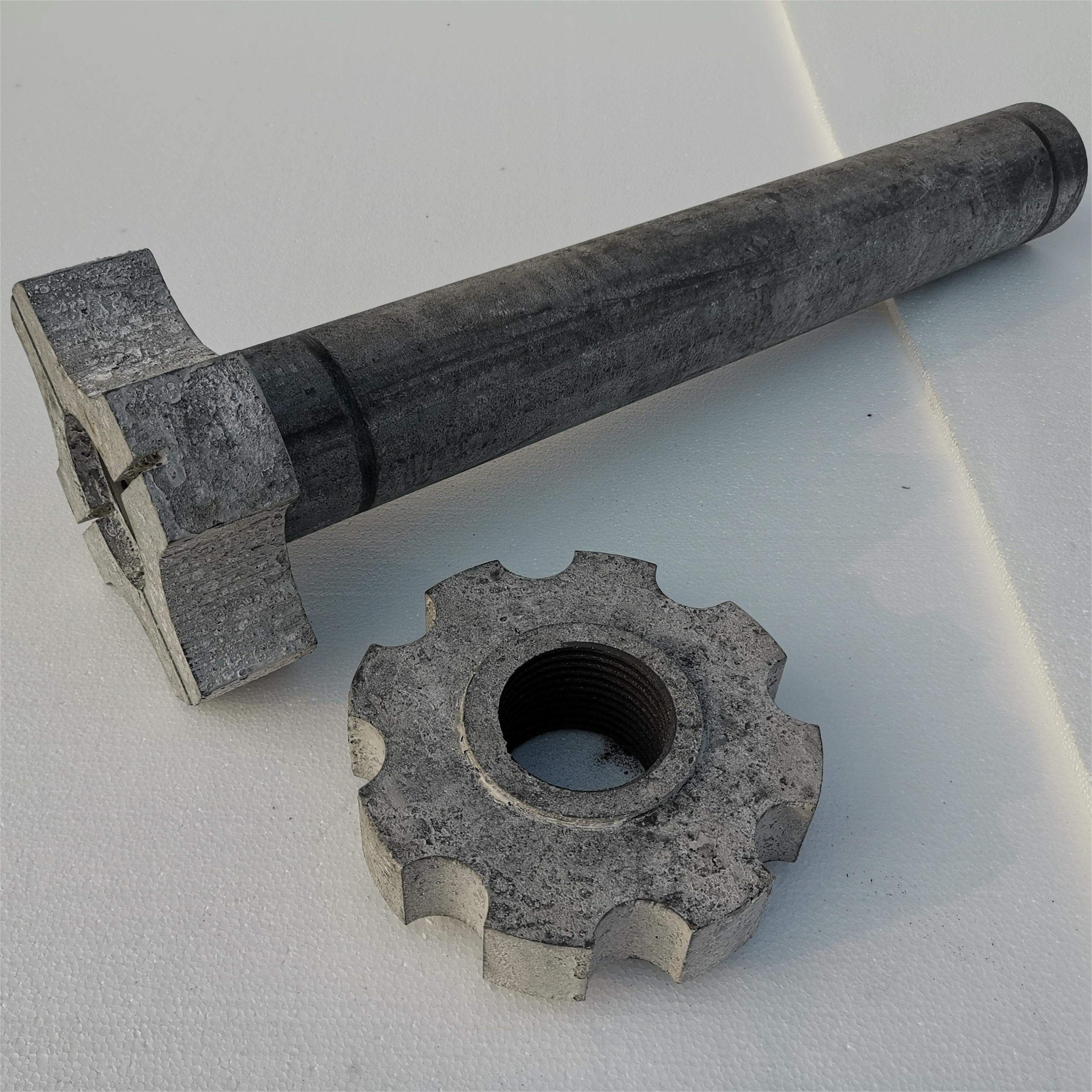
Post time: May-29-2024