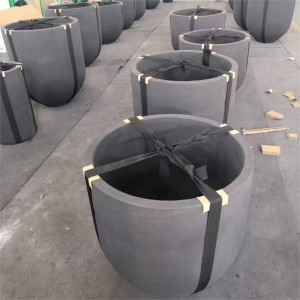
The manufacturing technology of graphite crucibles for smelting copper is undergoing a revolution. This process uses the world's most advanced cold isostatic pressing method and is formed under a high pressure of 600MPa to ensure that the internal structure of the crucible is uniform and defect-free and has extremely high strength. This innovation not only improves the performance of the crucible, but also makes a major breakthrough in energy conservation and environmental protection.
Advantages of cold isostatic pressing
Internal structure is uniform and defect-free
Under high-pressure molding, the internal structure of the copper-graphite crucible is extremely uniform without any defects. This is in stark contrast to traditional cutting methods. Due to the lower pressure, traditional methods inevitably lead to internal structural defects that affect its strength and thermal conductivity.
High strength, thin crucible wall
The cold isostatic pressing method significantly improves the strength of the crucible under high pressure. The greater strength allows the crucible walls to be made thinner, thereby increasing thermal conductivity and reducing energy consumption. Compared with traditional crucibles, this new type of crucible is more suitable for efficient production and energy saving requirements.
Excellent thermal conductivity and low energy consumption
The high strength and thin-walled structure of molten copper graphite crucibles result in significantly better thermal conductivity compared to conventional crucibles. Improving thermal conductivity means that heat can be transferred more evenly and quickly during the smelting process of aluminum alloys, zinc alloys, etc., thereby reducing energy consumption and improving production efficiency.
Comparison with traditional manufacturing methods
Limitations of cutting methods
Most of the domestically produced graphite crucibles are made by cutting and then sintering. This method results in uneven, defective, and low-strength internal structures due to lower pressure. In addition, it has poor thermal conductivity and high energy consumption, making it difficult to meet the requirements of modern industry for high efficiency and energy saving.
Disadvantages of imitators
Some manufacturers imitate the cold isostatic pressing method to produce crucibles, but due to insufficient manufacturing pressure, most of them produce silicon carbide crucibles. These crucibles have thicker walls, poor thermal conductivity, and high energy consumption, which are far from the real molten copper graphite crucibles produced by cold isostatic pressing.
Technical principles and applications
In the smelting process of aluminum and zinc alloys, the oxidation resistance and thermal conductivity of the crucible are crucial factors. Crucibles manufactured using the cold isostatic pressing method place special emphasis on oxidation resistance while avoiding the adverse effects of fluoride-containing fluxes. These crucibles maintain excellent performance at high temperatures without contaminating the metal, significantly improving durability.
Application in aluminum alloy smelting
Graphite crucible plays a vital role in the melting of aluminum alloys, especially in the production of die castings and castings. The melting temperature of aluminum alloy is between 700°C and 750°C, which is also the temperature range where graphite is easily oxidized. Therefore, graphite crucibles produced by cold isostatic pressing place special emphasis on oxidation resistance to ensure excellent performance at high temperatures.
Designed for different melting methods
Graphite crucible is suitable for a variety of smelting methods, including single-furnace smelting and smelting combined with heat preservation. For aluminum alloy castings, the crucible design needs to meet the requirements of preventing H2 absorption and oxide mixing, so a standard crucible or a large-mouth bowl-shaped crucible is used. In centralized smelting furnaces, tilting crucible furnaces are usually used to recycle smelting waste.
Comparison of performance features
High density and thermal conductivity
The density of graphite crucibles manufactured by cold isostatic pressing is between 2.2 and 2.3, which is the highest density among crucibles in the world. This high density gives the crucible optimal thermal conductivity, significantly better than other brands of crucibles.
Glaze and corrosion resistance
The surface of the molten aluminum graphite crucible is covered with four layers of special glaze coating, which, combined with the dense molding material, greatly improves the corrosion resistance of the crucible and extends its service life. In contrast, domestic crucibles have only a layer of reinforced cement on the surface, which is easily damaged and causes premature oxidation of the crucible.
Composition and thermal conductivity
The molten copper graphite crucible uses natural graphite, which has excellent thermal conductivity. In contrast, domestic graphite crucibles use synthetic graphite, reduce the graphite content to reduce costs, and add a large amount of clay for molding, so the thermal conductivity is significantly reduced.
Packaging and application areas
Packing
Molten copper graphite crucible is usually bundled and packaged with straw rope, which is a simple and practical method.
Expansion of application fields
With the continuous advancement of technology, the application fields of graphite crucibles continue to expand. Especially in the production of aluminum alloy die castings and castings, graphite crucibles are gradually replacing traditional cast iron pots to meet the production requirements of high-quality automotive parts.
in conclusion
The application of cold isostatic pressing method has brought the performance and efficiency of copper-graphite crucible smelting to a new level. Whether it is the uniformity, strength or thermal conductivity of the internal structure, it is significantly better than traditional manufacturing methods. With the widespread application of this advanced technology, the market demand for graphite crucibles will continue to expand, driving the entire industry toward a more efficient and environmentally friendly future.
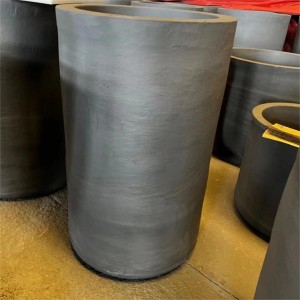
Post time: Jun-05-2024