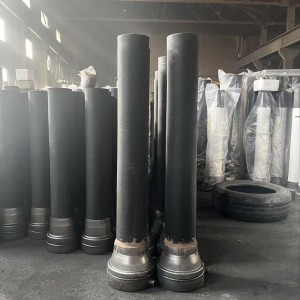
In the steel continuous casting process, the high temperature molten steel flows from ladle to crystallizer, which goes through a series of key components, and these components are stable and unreliable, which directly determines whether the continuous casting production can be smooth and the quality of the billet is good. Today, let's take a good look at several key refractory materials in the continuous casting process, including Tundish Shroud,Submerged Nozzle,Refractory Nozzle,ladle shroud,tundish refractory,tundish refractories,ladle nozzle,submerged entry nozzle, and analyze what role they play in the continuous casting process, what problems they face, and what direction they will develop in the future.
Tundish Shroud: connecting top to bottom, isolated oxidation
Tundish Shroud of the tundish is a key component connecting the tundish and the mold. It is like a bridge, guiding the molten steel from the tundish to the mold steadily, and also shoulders an important mission - preventing the molten steel from contacting the air and avoiding secondary oxidation. Usually, the tundish long nozzle is made of high aluminum or aluminum carbon refractory materials, which give it good thermal shock resistance, erosion resistance and erosion resistance, so that it can stick to its position in harsh working environments.
Challenges faced
Thermal shock damage: During continuous casting, the long water mouth of the tundish has to withstand drastic temperature changes, and it is hot for a while and cold for a while, which is easy to produce thermal stress, and after a long time, cracks may appear, or even direct fracture.
Molten steel erosion: high-temperature molten steel is like an "erosion master", constantly scouring the inner wall of the long nozzle, and the service life of the long nozzle is therefore shortened.
Alumina blockage: The alumina inclusions in the molten steel are like a "small trick", especially easy to deposit in the inner wall of the long water mouth, blocking the channel, and the flow of molten steel is not smooth.
Development trend
Development of new refractories: Now nanotechnology is getting more and more powerful, refractory materials prepared with nanotechnology have higher strength, thermal shock resistance and erosion resistance are better, and the future is expected to play a big role in the tundish long water mouth.
Optimized structural design: By improving the shape and size of the long nozzle, the molten steel can flow more smoothly and the alumina deposition can be reduced significantly.
Application of advanced coating technology: Coating the inner wall of the long nozzle with anti-oxidation and anti-erosion coating is like putting on a layer of "protective clothing", and the service life can be greatly extended.
Submerged Nozzle: Precise control to promote solidification
The submerged nozzle is installed above the mold and is a key component for injecting molten steel into the mold. Its role is not small, not only can control the flow rate and direction of molten steel, prevent molten steel splashing and secondary oxidation, but also promote the uniform solidification of molten steel in the mold, which has an important impact on the quality of casting billet.
Challenges faced
Molten steel erosion and erosion: Long-term immersion in high-temperature molten steel, the immersion nozzle withstands serious erosion and erosion, just like the soldier who holds fast in the wind and rain, and the pressure is huge.
Thermal stress cracking: Like the tundish long nozzle, it also has to withstand drastic temperature changes, and thermal stress can easily lead to cracks.
Alumina plugging: This is also a perennial problem, the deposition of alumina inclusions will affect the normal flow of molten steel.
Development trend
Development of high-performance refractory materials: such as zirconium carbon, magnesium carbon and other high-performance refractory materials, can improve the erosion resistance and thermal shock resistance of the immersion nozzle, making it more durable.
Optimize the nozzle structure: reasonably design the shape and size of the nozzle, improve the flow state of molten steel, and reduce the deposition of alumina.
Application of electromagnetic braking technology: Applying an electromagnetic field near the submerged nozzle is like installing a "controller" on the molten steel, which can control the flow rate and direction of the molten steel and reduce the scouring of the molten steel on the nozzle.
Refractory Nozzle: control molten steel, smooth transportation
The refractory nozzle is installed at the bottom of the ladle, which is mainly responsible for controlling the outflow speed and flow rate of molten steel, preventing splashing and secondary oxidation of molten steel, ensuring that molten steel can flow smoothly into the tundish, and laying a good foundation for the subsequent continuous casting work.
Challenges faced
Molten steel erosion and erosion: long-term contact with high temperature molten steel, withstand serious erosion and erosion, its performance is a great test.
Thermal stress cracking: Severe temperature change is easy to produce thermal stress, resulting in cracks, affecting its normal work.
Alumina clogging: alumina inclusions deposit on the inner wall of the nozzle, which will hinder the flow of molten steel and reduce production efficiency.
Development trend
Development of new refractory materials: The use of silicon carbide, silicon nitride and other high-performance refractory materials, improve its corrosion resistance and thermal shock resistance, extend the service life.
Optimize the nozzle structure: Improve the shape and size of the nozzle to make the flow of molten steel more reasonable and reduce the deposition of alumina.
Application of advanced coating technology: Coating the inner wall of the water outlet with anti-oxidation and anti-erosion coating to enhance its protection ability.
Ladle Shroud: connecting ladle, isolate air
The ladle shroud is connected with the ladle and tundish, which is used to guide the molten steel from the ladle to the tundish, prevent the molten steel from contacting with the air, avoid secondary oxidation, and ensure the purity of the molten steel. It is usually made of high aluminum or aluminum carbon refractory material, with good thermal shock resistance, erosion resistance and erosion resistance.
Challenges faced
Thermal shock damage: the temperature changes dramatically in the continuous casting process, which is easy to produce thermal stress, resulting in cracks and even fractures.
Molten steel erosion: The erosion and erosion of high-temperature molten steel will shorten its service life.
Alumina plugging: alumina inclusions in molten steel deposit on the inner wall of the long nozzle, affecting the flow of molten steel.
Development trend
Development of new refractory materials: Refractory materials prepared by nanotechnology are expected to improve their performance.
Optimize the structure design: improve the shape and size of the long nozzle, improve the flow state of molten steel.
Apply advanced coating technology: Apply coating to extend its service life.
Tundish Refractory: bearing molten steel, stable structure
Tundish refractory material is used to build tundish lining, its main function is to withstand the erosion and erosion of high temperature molten steel, maintain the structural stability of tundish, and provide a safe and reliable "temporary residence" for molten steel. It is usually made of high aluminum, magnesium, zirconium and other refractory materials, with good corrosion resistance, thermal shock resistance and spalling resistance.
Challenges faced
Molten steel erosion and erosion: long-term contact with high temperature molten steel, bearing serious erosion and erosion.
Thermal stress cracking: Temperature changes easily produce thermal stress, leading to cracks.
Alumina deposition: Alumina inclusions in molten steel are deposited on its surface, affecting the quality of molten steel.
Development trend
Development of high-performance refractory materials: Using nanotechnology to prepare refractory materials to improve their performance.
Optimize the masonry process: improve the masonry process, improve its integrity and stability.
Application of advanced coating technology: Coating for extended service life.
Ladle Nozzle: control flow, ensure delivery
The ladle nozzle is installed at the bottom of the ladle, which is responsible for controlling the outflow speed and flow rate of the ladle, preventing the splashing and secondary oxidation of the ladle, and ensuring that the ladle can flow smoothly into the tundish, which is an important barrier in the ladle conveying process.
Challenges faced
Molten steel erosion and erosion: long-term withstand high temperature molten steel erosion and erosion.
Thermal stress cracking: temperature changes lead to thermal stress, which is easy to crack.
Alumina clogging: Deposition of alumina inclusions affects the flow of molten steel.
Development trend
Development of new refractory materials: The use of silicon carbide, silicon nitride and other high-performance refractory materials to improve their performance.
Optimize the nozzle structure: improve the shape and size, improve the flow state of molten steel.
Application of advanced coating technology: Coating for extended service life.
Immersion inlet: guide molten steel and promote solidification
The immersion inlet is installed above the mold, and its main function is to control the flow rate and direction of the molten steel, prevent the splashing and secondary oxidation of the molten steel, and promote the uniform solidification of the molten steel in the mold, which plays a key role in the quality of the casting billet.
Challenges faced
Molten steel erosion and erosion: long-term immersion in high-temperature molten steel, bearing serious erosion and erosion.
Thermal stress cracking: Temperature changes produce thermal stress, which can easily lead to cracks.
Alumina blockage: Similar to the tundish long nozzle, it also faces the problem of alumina blockage.
Development trend
Development of high-performance refractory materials: The use of zirconium carbon, magnesium carbon and other high-performance refractory materials to improve its corrosion resistance and thermal shock resistance.
Optimize the nozzle structure: improve the shape and size, improve the flow state of molten steel.
Application of electromagnetic braking technology: electromagnetic field is applied to control the flow rate and direction of molten steel and reduce the flushing of molten steel to the nozzle.
Post time: Feb-20-2025