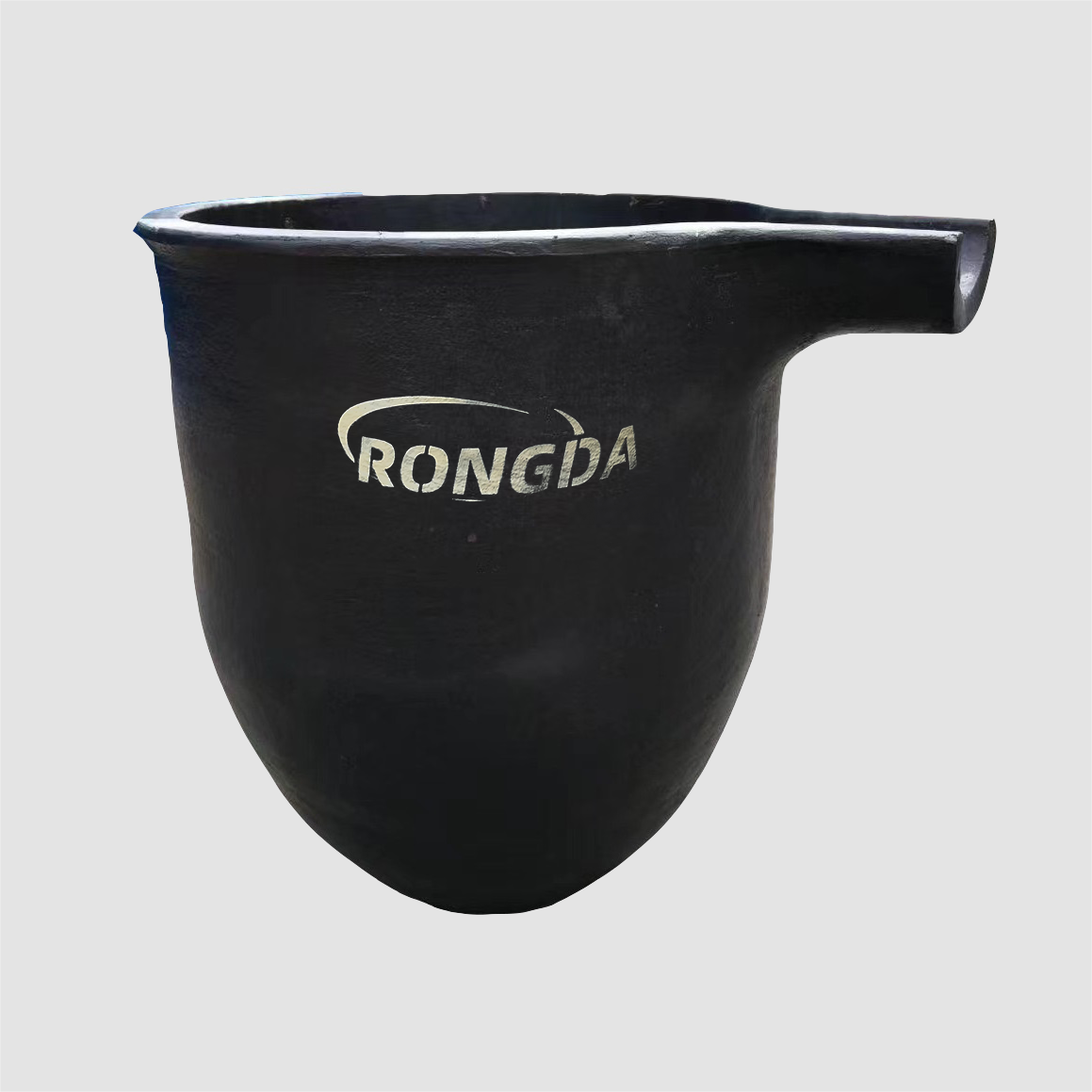
A crucible melting pot, an indispensable tool in the realm of metalworking, casting, and materials science, serves as a foundational element for melting and handling various metals at high temperatures. This specialized container, designed to withstand extreme heat, is pivotal for transforming solid metals into liquid form for casting, alloying, and other processes. This article aims to explore the nature, construction, and diverse applications of crucible melting pots, integrating a variety of keywords to enhance readability and meet Google's SEO ranking criteria.
Understanding Crucible Melting Pots
At its core, a crucible melting pot is a vessel made from materials capable of enduring temperatures significantly higher than the melting points of metals or alloys being processed. These containers are engineered to maintain structural integrity and chemical inertness, even when subjected to the rigorous thermal environments typical in foundries, laboratories, and artisan workshops.
Materials Used in Crucible Manufacturing
- Graphite: Offers excellent thermal conductivity and resistance to thermal shock, making it ideal for melting precious metals.
- Silicon Carbide (SiC): Renowned for its high thermal stability and resistance to wear, SiC crucibles are suited for melting ferrous metals.
- Alumina (Al2O3): Chosen for its refractoriness and resistance to corrosion, alumina crucibles are perfect for high-purity melts.
- Clay-Graphite: A cost-effective option that combines the thermal efficiency of graphite with the structural strength of clay, suitable for general-purpose metal casting.
- Boron Nitride: Utilized for its exceptional thermal shock resistance and lubricity, ideal for specialized applications requiring the handling of molten metals without sticking.
- High Melting Point: Crucible melting pots are selected based on their ability to surpass the melting temperatures of the content without degrading.
- Chemical Stability: They must not react with the metal or alloy being melted to prevent contamination.
- Thermal Shock Resistance: The ability to withstand rapid temperature changes is crucial for preventing cracks and ensuring longevity.
- Capacity and Shape: The size and design of crucible melting pots vary, tailored to specific melting processes and volume requirements.
Key Features and Considerations
Applications Across Various Fields
Crucible melting pots find their use in a multitude of settings, showcasing their versatility:
- Metal Casting: Essential in foundries for melting and pouring metals into molds to create components for automotive, aerospace, and machinery industries.
- Jewelry Making: Used by jewelers for melting precious metals for casting rings, necklaces, and other adornments.
- Research and Development: Scientists and engineers utilize crucible melting pots for experimental alloys and materials research, benefiting from the controlled melting environment they provide.
- Educational Purposes: In academic settings, these tools assist in teaching the principles of metallurgy and materials science, offering hands-on experience with melting and casting processes.
Conclusion
A crucible melting pot is more than just a container; it's a critical instrument that facilitates the transformation of metals from solid to liquid, enabling casting, alloying, and experimentation. The selection of a crucible melting pot depends on the metal to be melted, the melting environment, and the specific requirements of the process it supports. With advancements in materials technology and manufacturing, the capabilities and applications of crucible melting pots continue to expand, playing a vital role in the progression of metalworking and materials engineering disciplines. Whether for industrial production, artisanal crafting, or scientific exploration, the crucible melting pot remains a symbol of transformation and creation in the manipulation of materials.
Post time: Mar-01-2024