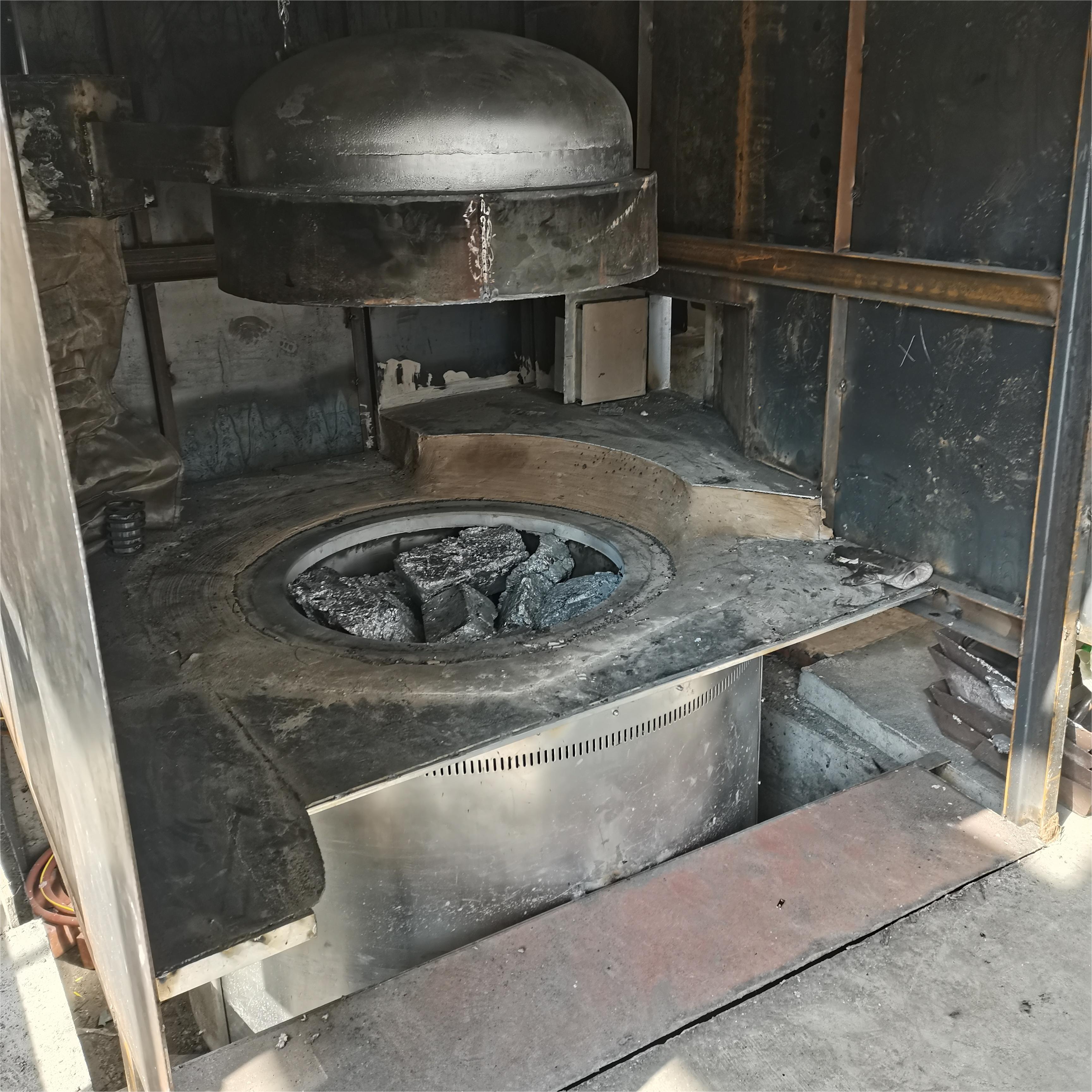
A melting crucible furnace stands as a cornerstone in the metallurgical and materials science industries, providing a pivotal function in the melting of metals, alloys, and other materials. This specialized furnace type is designed to reach high temperatures, necessary for melting various metals, while safely containing them within a crucible—a container made from materials capable of withstanding extreme heat. This article delves into the essence, functionality, and broad applications of melting crucible furnaces, incorporating diverse keywords to ensure readability and adherence to Google's SEO ranking rules.
Understanding Melting Crucible Furnaces
At its core, a melting crucible furnace is a high-temperature oven designed to melt metals like aluminum, copper, gold, silver, and steel. It operates by heating a crucible inside which the metal is placed, utilizing various fuel sources, including gas, electricity, or induction, to achieve the necessary temperatures for melting. The choice of crucible material—such as graphite, silicon carbide, or alumina—depends on the melting point of the metal and the furnace's operating conditions.
Key Features and Benefits
- High-Temperature Capability: These furnaces can reach temperatures well above the melting points of most metals, often exceeding 1,000°C (1,832°F) for metals like aluminum, and going much higher for metals with higher melting points.
- Versatility: They are suitable for a wide range of applications, from small-scale jewelry making to large-scale industrial metal casting.
- Efficiency: Modern melting crucible furnaces are designed for high energy efficiency, with insulation and technology that minimize heat loss and maximize melting speed.
- Control: They offer precise temperature control, which is crucial for achieving the desired properties in the melted metal, such as purity and alloy composition.
Applications Across Industries
Melting crucible furnaces find their application in numerous fields, underscoring their versatility and indispensability:
- Metalworking and Casting: They are essential in foundries for melting metals before casting them into molds to create tools, automotive parts, sculptures, and jewelry.
- Recycling: These furnaces play a critical role in the recycling of metals, where scrap metal is melted down and reused, contributing to sustainable manufacturing practices.
- Research and Development: In laboratories, small-scale melting crucible furnaces are used for material testing and the development of new alloys and composites.
- Education: Academic institutions utilize these furnaces for teaching metallurgy, materials science, and engineering principles.
Selecting the Right Melting Crucible Furnace
Choosing the appropriate melting crucible furnace involves considering several factors:
- Temperature Requirements: The furnace must reach the melting point of the material being processed.
- Volume and Throughput: The size of the crucible and the furnace's design should match the volume of metal to be melted and the desired speed of production.
- Fuel Source: Electric, gas, and induction furnaces offer different advantages in terms of efficiency, control, and environmental impact.
- Material Compatibility: The crucible material must be compatible with the metal being melted to prevent contamination.
Conclusion
A melting crucible furnace is an essential piece of equipment in the field of metal processing, offering the capability to melt a variety of metals for diverse applications. From crafting fine jewelry to forging automotive parts and advancing the frontiers of materials science, these furnaces play a pivotal role in transforming raw materials into valuable products. Understanding the functionality and applications of melting crucible furnaces illuminates the importance of this technology in industrial, academic, and artistic endeavors, showcasing its contribution to innovation and sustainability in metalworking and beyond.
Post time: Feb-26-2024