Pouring Crucible for Pouring Molten Copper
Key Features:
- High-Temperature Resistance:
- The pouring crucible is crafted from advanced materials such as silicon carbide or graphite, which offer excellent thermal resistance. These materials can withstand the high temperatures of molten metals, ensuring the crucible's longevity and reliability.
- Efficient Pouring Mechanism:
- The crucible is designed with a spout or tapered edge, enabling smooth and controlled pouring. This minimizes spillage and reduces the risk of accidents, ensuring the molten metal is transferred accurately into the mold.
- Enhanced Durability:
- Built to endure frequent exposure to intense heat, the crucible is highly durable and resists cracking, deformation, and thermal stress, ensuring long service life even in demanding conditions.
- Capacity Range:
- Pouring crucibles come in various sizes and capacities to meet the specific needs of different casting operations. Whether for small-scale foundries or large industrial production lines, these crucibles can accommodate diverse requirements.
- Customizable Designs:
- Depending on the application, pouring crucibles can be tailored with specific features such as handles for manual operation or tilting mechanisms for automated systems, enhancing ease of use and safety during operation.
- Thermal Conductivity:
- The materials used in the crucible allow for excellent thermal conductivity, which helps maintain the molten metal’s fluidity during the pouring process, reducing heat loss and improving casting quality.
Know-How: Isostatic Pressing in Crucible Production
The isostatic pressing process is what sets our pouring crucibles apart. Here’s why it matters:
Isostatic Pressing Benefits | Traditional Methods |
---|---|
Uniform density | Inconsistencies in structure |
Higher resistance to cracking | Lower resistance to thermal stress |
Enhanced thermal properties | Slower heat transfer |
This process applies even pressure to all sides of the crucible during manufacturing, resulting in a product that is stronger, more reliable, and able to withstand the extreme conditions of aluminum melting. Compared to traditional methods, isostatic pressing delivers a superior product, offering better thermal conductivity, crack resistance, and overall durability.
Advantages:
- Precision Pouring:
- The crucible’s design ensures controlled flow of molten metal, reducing wastage and achieving precise filling of molds, leading to high-quality castings with fewer defects.
- Safety in Operation:
- By offering a stable and controlled pouring mechanism, the risk of spills or splashes is minimized, protecting workers and equipment from the dangers associated with handling molten metals.
- Compatibility with Various Metals:
- Pouring crucibles can be used with a wide range of molten metals, including aluminum, copper, gold, silver, and brass. This versatility makes them ideal for use in various industries such as jewelry making, automotive casting, and heavy industrial production.
- Thermal Shock Resistance:
- The materials used to manufacture these crucibles are highly resistant to thermal shock, meaning they can withstand rapid temperature changes without cracking or degrading, which ensures reliable performance over time.
- Cost-Effective:
- The longevity and durability of the pouring crucible reduce the need for frequent replacements, making it a cost-effective option for foundries looking to optimize their operational efficiency.
Applications:
- Metal Casting Industry: Widely used in foundries for casting metals into molds with precision.
- Jewelry Manufacturing: Ideal for pouring precious metals like gold and silver during jewelry production.
- Automotive and Aerospace: Used in the casting of engine parts and other critical components that require high-quality metalwork.
- Industrial Metal Production: Suitable for transferring molten metals during various stages of metalworking and production processes.
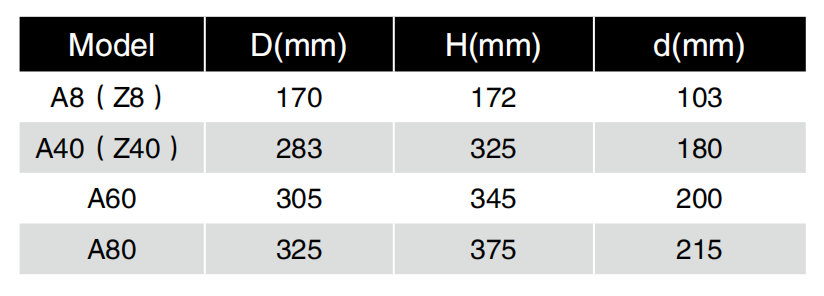